Industry

Manufacturing FSL - Implementation Success story
Manufacturing
Products
Service Cloud
Field Service Lightning
Overview
- Dynavac Pvt Ltd Manufactures industrial and commercial cleaning equipment and dust collection systems for professionals, companies, and businesses since 1989.
- First industrial vacuum cleaner manufacturer in India.
- Operates in multiple locations across APAC region and business type is B2B and B2C.
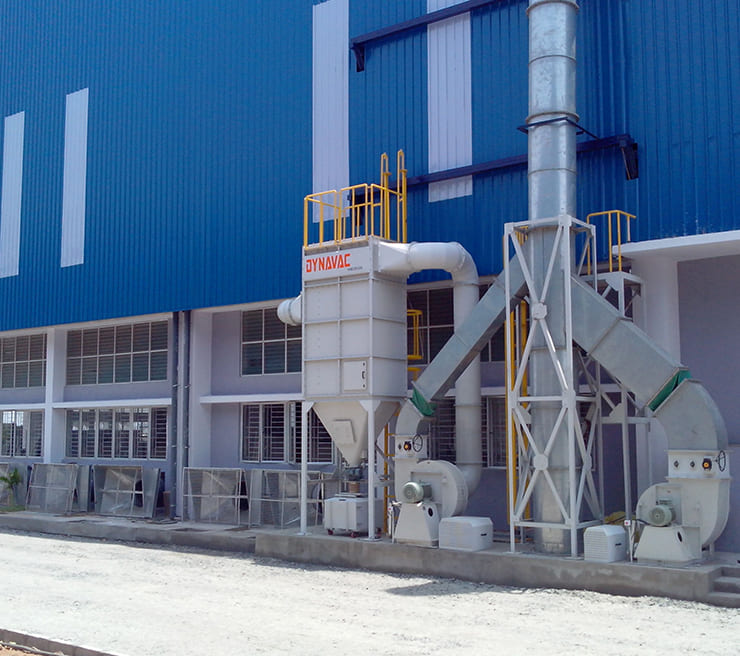
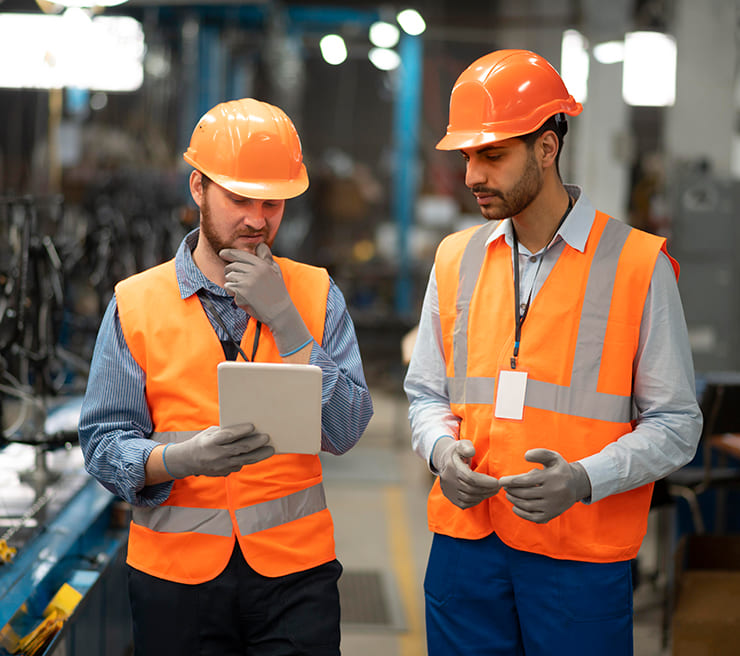
Problem Statement
As the Business grew, taking on clients, expanding its business and reaching new territories, Dynavac was facing challenges as follows.
- Struggling to manage their support system with local excel based system for repairs.
- Regular health check need to be scheduled for maintenance of their implemented projects. In efficient utilization of their technical resources and planning for services and health checks are time consuming job.
- Identifying the rightly skilled resource and prioritize the customer need are challenging with phone calls and excel based system.
- Technicians are struggled with lack of communications from the team lead on the work allocations on day to day.
Solution
Inno Valley Works analyzed the Dynavac paint points and proposed Salesforce service cloud with Field Service Lightning.
- Service cloud implemented to receive all their customer issues into cases and queue them for fixes based on the priority and technical issues.
- Field service lightning dispatcher console implemented for Resource allocator to find the work orders and the right skilled resource with their availability to allocate the job.
- The dispatcher console Gantt view also capable to identify the resource utilizations and availability, and filter based on the region wise and skills.
- Field service lightning mobile app implemented for field service technicians to find their day to day jobs and get notified on the updates.
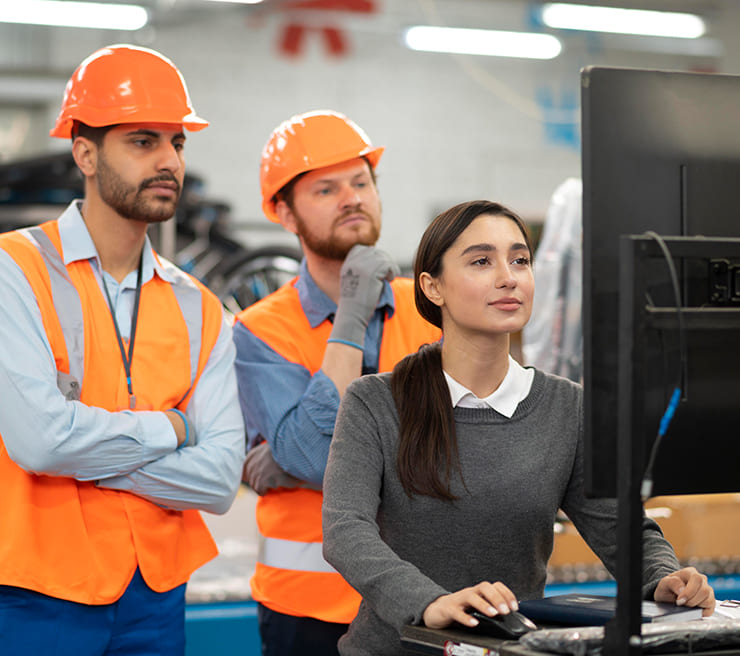
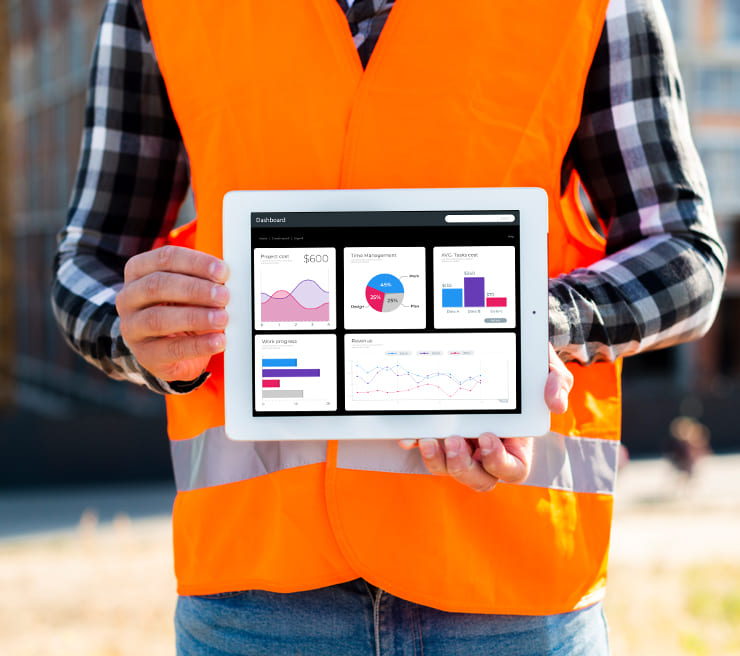
Result
- Streamlined Case management without missing any customer issues and solved based on the priority.
- Single view of all resources allocations and better utilization.
- Automated way of skill based resource allocations from the same regions saved technicians traveling time and increased productivity upto 25%.
- Management and supervisors can make sure the cases are solved ontime with the technicians mobile app check in / check out.
- Communication gaps are eliminated between work dispatcher and field technicians.
- Get the overview of field technicians allocations and work schedule at any point of time from single view.
- Well executed the health checks on the machineries without any deviations and delays on the schedule